Page 2 of 3
Re: Single point threading titanium tube
Posted: Fri Apr 01, 2016 7:43 pm
by Historian
Fulmen wrote:I''ve only threaded one or two parts in titanium (Grade 2) with carbide tooling but they came out perfect on the first try. I don't do the 30° nonsense, just feed straight in. Speed is appr 100rpm with foot brake and locked half nuts.
Wow!!
This is a surprising new approach which is the antithesis
from all my exposure to master tool & die maker
machinists starting in 1956.
One of the reasons given was that as you deepened the thread
the tool was engaging two simultaneous cutting sides
rather than one and in turn increasing friction and galling.
Hope our expert trust will chime in on this.
Sure would be simpler if true.
Most interesting.
Re: Single point threading titanium tube
Posted: Fri Apr 01, 2016 8:04 pm
by curtistactical
Historian wrote:Fulmen wrote:I''ve only threaded one or two parts in titanium (Grade 2) with carbide tooling but they came out perfect on the first try. I don't do the 30° nonsense, just feed straight in. Speed is appr 100rpm with foot brake and locked half nuts.
Wow!!
This is a surprising new approach which is the antithesis
from all my exposure to master tool & die maker
machinists starting in 1956.
One of the reasons given was that as you deepened the thread
the tool was engaging two simultaneous cutting sides
rather than one and in turn increasing friction and galling.
Hope our expert trust will chime in on this.
Sure would be simpler if true.
Most interesting.
You are right Historian, when you feed in at 30deg you are cutting with the front cutting edge only. I always do it this way on the manual lathe but on the cnc I just do a straight in feed. On fine threads where the threads are pretty shallow you can get away with just a straight in feed but as the threads gets coarser there is a lot more surface contacting the tool and you will get chatter in the threads if you are cutting with both sides of the tool. The correct way is using the compound on 29.5-30.0 deg to in feed and the cross slide to keep your zero set to return to each pass.
Joe
Re: Single point threading titanium tube
Posted: Sat Apr 02, 2016 2:56 am
by Fulmen
curtistactical wrote:The correct way
The correct way is whatever gets the job done. For coarse threads, hard materials or small machines the 30° trick can help, but most of the time I've managed fine with feeding straight in.
Re: Single point threading titanium tube
Posted: Sat Apr 02, 2016 6:14 am
by Historian
Thank you Curtistactical for the clarification.
Regrettably, not owning a CNC but hand cranking
lathe I shall stick to 29.5º, though for a test I shall
try straight in on a 32 tpi thread. It will be fun
setting up the new gear combinations on the 618
as a mental exercise, deriving requisite gear ratios from first
principles.
Where is my Post Versalog?
Fireman, appreciation for your outstanding presentations.
Stellar, Sir.
Re: Single point threading titanium tube
Posted: Sat Apr 02, 2016 7:07 am
by curtistactical
Fulmen wrote:curtistactical wrote:The correct way
The correct way is whatever gets the job done. For coarse threads, hard materials or small machines the 30° trick can help, but most of the time I've managed fine with feeding straight in.
I say "the correct way" because if you are taught by an actual machinist this is how he will teach you to do it. Not trying to start an argument just saying the "30deg trick" isn't a trick it is how it is supposed to be done. Not only does this apply way less cutting force on the tool it keeps the pressure pushing against the half nut making up for any play that it has, when you are cutting with both sides of the tool it will allow the tool to jump creating an inconsistent pitch to some degree. The CNC lathe has ball screw which allows you to straight in feed because there is no backlash. The more wore out your lathe is the more this will be noticed. If you would like to do a test to see this, cut a 10tpi thread, you will notice when the tool enters the first thread as you are close to finish if you are straight in feeding the carriage will be jerked around, if you are in feeding on 30deg it will enter smoothly.
Joe
Re: Single point threading titanium tube
Posted: Sat Apr 02, 2016 8:17 am
by 300sniper
I still feed at 30 degrees on the turning center. It doesn't take any longer to program.
Re: Single point threading titanium tube
Posted: Sat Apr 02, 2016 8:37 am
by Fulmen
curtistactical wrote:because if you are taught by an actual machinist
Actually I was taught by a skilled machinist as well. I'm not saying it's wrong to feed at an angle, just that it isn't mandatory for all jobs. It depends on the tooling, setup and material, but for plain steel and say <2-2,5mm pitch (about as coarse as I've ever needed) I've never seen the need for it in my 12x36. Your mileage may wary of course.
Re: Single point threading titanium tube
Posted: Sun Apr 10, 2016 11:18 pm
by yondering
curtistactical wrote:Fulmen wrote:curtistactical wrote:The correct way
The correct way is whatever gets the job done. For coarse threads, hard materials or small machines the 30° trick can help, but most of the time I've managed fine with feeding straight in.
I say "the correct way" because if you are taught by an actual machinist this is how he will teach you to do it. Not trying to start an argument just saying the "30deg trick" isn't a trick it is how it is supposed to be done. Not only does this apply way less cutting force on the tool
it keeps the pressure pushing against the half nut making up for any play that it has, when you are cutting with both sides of the tool it will allow the tool to jump creating an inconsistent pitch to some degree. The CNC lathe has ball screw which allows you to straight in feed because there is no backlash. The more wore out your lathe is the more this will be noticed. If you would like to do a test to see this, cut a 10tpi thread, you will notice when the tool enters the first thread as you are close to finish if you are straight in feeding the carriage will be jerked around, if you are in feeding on 30deg it will enter smoothly.
Joe
Yes, exactly. The thread pitch can be inconsistent feeding straight in.
I started threading at 40 rpm, but then learned to thread at 250-300 rpm because that was the slowest my big lathe would go. Ain't no big deal once you get used to it.
Re: Single point threading titanium tube
Posted: Mon Apr 11, 2016 11:10 am
by Fulmen
I must admit that I've never noticed that, nor have I had any problems maintaining tight tolerances on threads.
Bottom line is: Why not try and make your own judgment? I've tried both, and for most jobs I just don't see any benefits in the 30° method.
Re: Single point threading titanium tube
Posted: Mon Apr 11, 2016 11:41 am
by Samson1044
I use the 30 deg setup when threading , it's always given better finish , tool life and way less deflection allowing consistent threads.
Even when using a big old heavy LeBlond lathe that I know is heavy and solid enough to make a full profile cut when I'm making something that is more than just a glorified bolt , light precise cuts are made. I use honed uncoated carbide cutters with MolyDee cutting oil at about 300 RPMs no matter what material.
I don't trust dials as I'm had them cause me some grief so every time I thread I set up a dial indicator on my tool post and one where my thread is gonna end. I find it easier to drop the half nut out quickly and accurately if I watch a dial run up to zero. I'm also anal about picking one number and cutting all my threads for a job with that number then I color it over and the next job uses a different number so everything wears evenly (just an OCD quirk I have)
here is some 24 tpi in a piece of grade 5 titanium , the male was cut from grade 5 as well and ended up a tight class 3 fit which is sketchy with titanium cause it galls so damn easy but with perfect threads its helps.
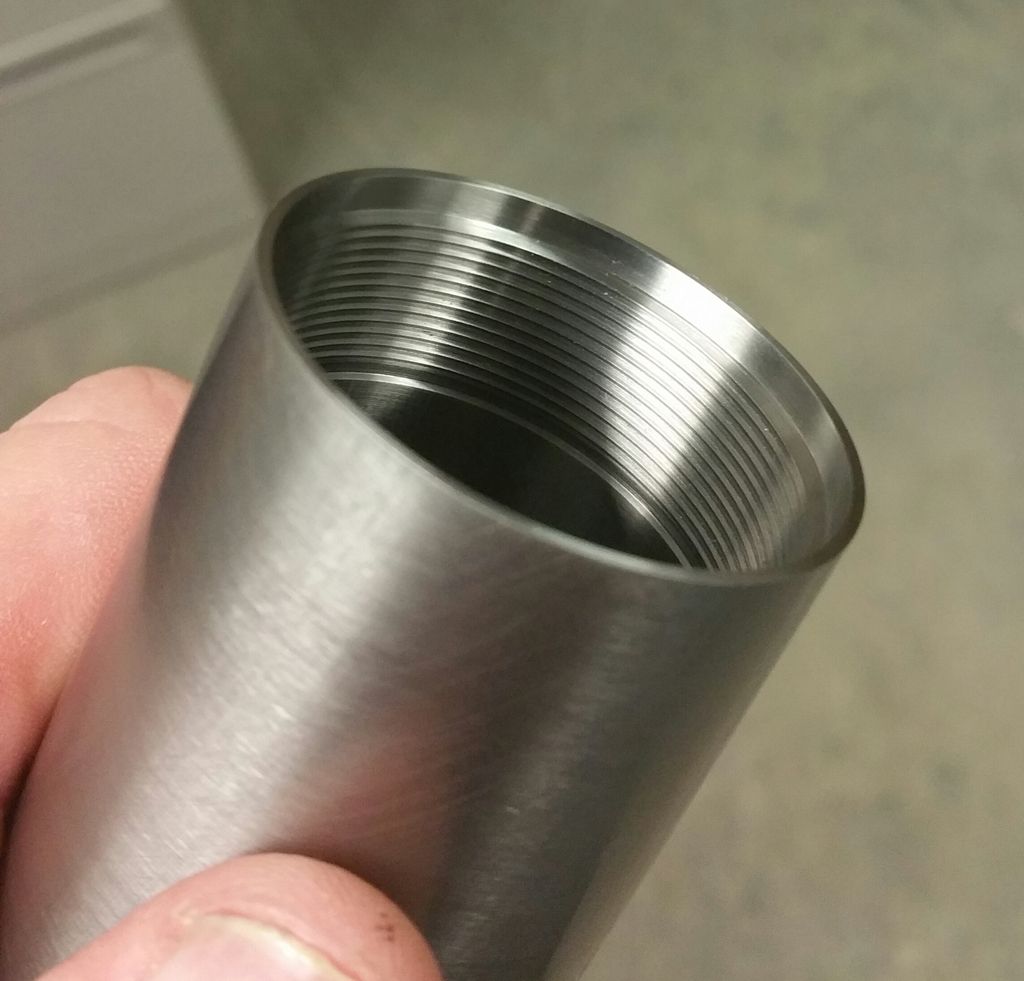
Re: Single point threading titanium tube
Posted: Mon Apr 11, 2016 4:56 pm
by Capt. Link.
curtistactical wrote:Samson1044 wrote:I use the 30 deg setup when threading , it's always given better finish , tool life and way less deflection allowing consistent threads.
Even when using a big old heavy LeBlond lathe that I know is heavy and solid enough to make a full profile cut when I'm making something that is more than just a glorified bolt , light precise cuts are made. I use honed uncoated carbide cutters with MolyDee cutting oil at about 300 RPMs no matter what material.
I don't trust dials as I'm had them cause me some grief so every time I thread I set up a dial indicator on my tool post and one where my thread is gonna end. I find it easier to drop the half nut out quickly and accurately if I watch a dial run up to zero. I'm also anal about picking one number and cutting all my threads for a job with that number then I color it over and the next job uses a different number so everything wears evenly (just an OCD quirk I have)
I say "the correct way" because if you are taught by an actual machinist this is how he will teach you to do it. Not trying to start an argument just saying the "30deg trick" isn't a trick it is how it is supposed to be done. Not only does this apply way less cutting force on the tool it keeps the pressure pushing against the half nut making up for any play that it has, when you are cutting with both sides of the tool it will allow the tool to jump creating an inconsistent pitch to some degree. The CNC lathe has ball screw which allows you to straight in feed because there is no backlash. The more wore out your lathe is the more this will be noticed. If you would like to do a test to see this, cut a 10tpi thread, you will notice when the tool enters the first thread as you are close to finish if you are straight in feeding the carriage will be jerked around, if you are in feeding on 30deg it will enter smoothly.
Joe
Joe brilliant summation of the facts.
Samson1044 Why UN-coated carbide +1 on mollydee.
I cut my first threads on a Le-blond I would dearly love to have her today.
I think the 29.5 set up is stiffer I know it runs cooler and with much less power and vibration.
Re: Single point threading titanium tube
Posted: Tue Apr 12, 2016 6:18 am
by Samson1044
Capt. Link. wrote:curtistactical wrote:Samson1044 wrote:I use the 30 deg setup when threading , it's always given better finish , tool life and way less deflection allowing consistent threads.
Even when using a big old heavy LeBlond lathe that I know is heavy and solid enough to make a full profile cut when I'm making something that is more than just a glorified bolt , light precise cuts are made. I use honed uncoated carbide cutters with MolyDee cutting oil at about 300 RPMs no matter what material.
I don't trust dials as I'm had them cause me some grief so every time I thread I set up a dial indicator on my tool post and one where my thread is gonna end. I find it easier to drop the half nut out quickly and accurately if I watch a dial run up to zero. I'm also anal about picking one number and cutting all my threads for a job with that number then I color it over and the next job uses a different number so everything wears evenly (just an OCD quirk I have)
I say "the correct way" because if you are taught by an actual machinist this is how he will teach you to do it. Not trying to start an argument just saying the "30deg trick" isn't a trick it is how it is supposed to be done. Not only does this apply way less cutting force on the tool it keeps the pressure pushing against the half nut making up for any play that it has, when you are cutting with both sides of the tool it will allow the tool to jump creating an inconsistent pitch to some degree. The CNC lathe has ball screw which allows you to straight in feed because there is no backlash. The more wore out your lathe is the more this will be noticed. If you would like to do a test to see this, cut a 10tpi thread, you will notice when the tool enters the first thread as you are close to finish if you are straight in feeding the carriage will be jerked around, if you are in feeding on 30deg it will enter smoothly.
Joe
Joe brilliant summation of the facts.
Samson1044 Why UN-coated carbide +1 on mollydee.
I cut my first threads on a Le-blond I would dearly love to have her today.
I think the 29.5 set up is stiffer I know it runs cooler and with much less power and vibration.
I use uncoated because I can hone it to a razor edge. I haven't been able to find a coated insert that was sharp enough to make a really light clean up pass. After I make my final .001" cut I run the tool back and make the pass again and it will always take a tiny bit more out of it , where with a coated tool it won't do that.
When making bigger stuff or stuff that doesn't require class 3 fit i'll run coated carbide and feed it strait in but with that kinda stuff my final cut is generaly at least a .002 cut. I've had to make quite a few pump shafts that require a 4"-6" stud ranging from 10-4 TPI
these nuts are from big storm water pumps that pump out our levee system don't here on da bayou. They are made from 410 SS and fully machined from a round stock all only using a big old lathe and a Bridgeport , each nut is slightly different and made to fit the shaft so its actually faster for me to make it on manual that have the dick heads in engineering to wright up a program for the CNC each time we have to make one. Joys of the maintaince world for the government.
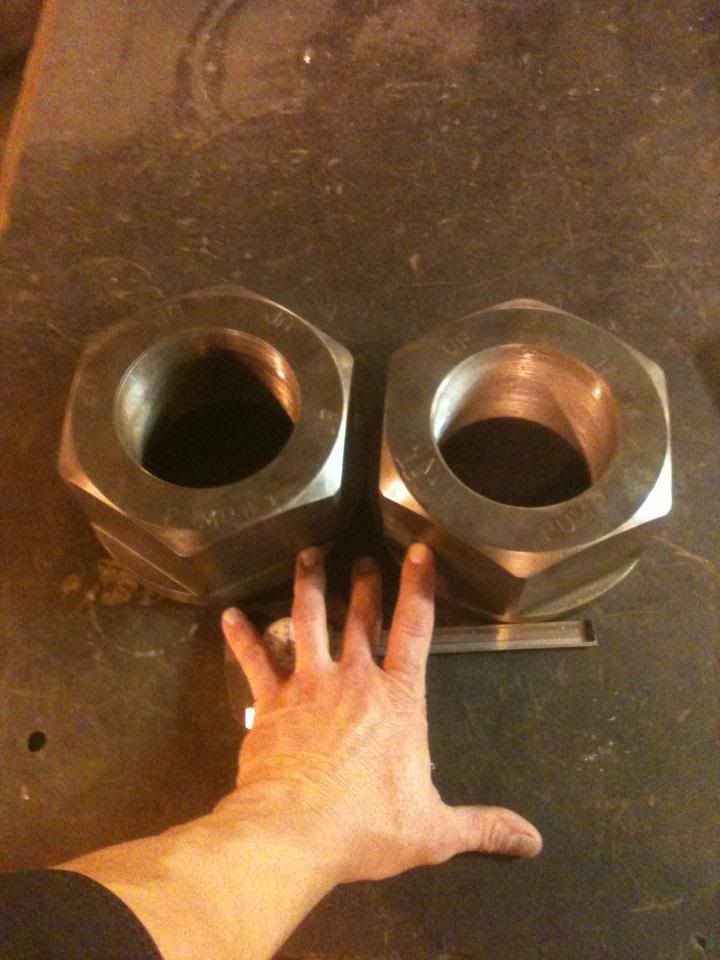
Re: Single point threading titanium tube
Posted: Tue Apr 12, 2016 7:01 am
by T-Rex
Damn Samson, you got some big nuts... errr Hands... errr nevermind

Re: Single point threading titanium tube
Posted: Tue Apr 12, 2016 7:02 am
by propeine
T-Rex wrote:I feel for you guys, turning your lathe by hand. That's pretty rough.
I just practiced, practiced, practiced, until I felt confident enough to do it on a real part.
My lathe goes down to 55rpm.
I now thread at about 220rpm.
You have to give yourself some credit and go for it.
Took yours and stan's advice last night. I got a new micro100 threading bar and needed to do some 1-20 threads. The carbide wasn't a big fan of back gear. It cut ok but they weren't the smoothest threads I've done. Backed it out an inch or so out of the hole, took it out of back gear and let er rip at 300rpm. They aren't samson quality but they are tight and smooth. The grit you see in there is lapping compound from final fitting to my few brakes.

Re: Single point threading titanium tube
Posted: Tue Apr 12, 2016 9:46 am
by Capt. Link.
Samson1044: My first job as a machinist was fabricating parts for local gov. Every day it was something new that they needed yesterday.I thought that may be the issue with the carbide but wanted to ask.
propeine: You might be out lathed by Samson but good tools like micro-100 and thin-bits etc are always a pleasure to use.Nice threading job

Re: Single point threading titanium tube
Posted: Tue Apr 12, 2016 9:50 am
by propeine
Capt. Link. wrote:Samson1044: My first job as a machinist was fabricating parts for local gov. Every day it was something new that they needed yesterday.I thought that may be the issue with the carbide but wanted to ask.
propeine: You might be out lathed by Samson but good tools like micro-100 and thin-bits etc are always a pleasure to use.Nice threading job

Good Cap you deserve credit for the lapping compound BTW. Leave it snug and lap it to fit. It wasn't originally directed at me but I did pick it up here. Worked wonderfully.
Re: Single point threading titanium tube
Posted: Tue Apr 12, 2016 10:49 am
by Samson1044
propeine wrote:T-Rex wrote:I feel for you guys, turning your lathe by hand. That's pretty rough.
I just practiced, practiced, practiced, until I felt confident enough to do it on a real part.
My lathe goes down to 55rpm.
I now thread at about 220rpm.
You have to give yourself some credit and go for it.
Took yours and stan's advice last night. I got a new micro100 threading bar and needed to do some 1-20 threads. The carbide wasn't a big fan of back gear. It cut ok but they weren't the smoothest threads I've done. Backed it out an inch or so out of the hole, took it out of back gear and let er rip at 300rpm. They aren't samson quality but they are tight and smooth. The grit you see in there is lapping compound from final fitting to my few brakes.

Threading at higher RPM can be unnerving at first but once you get the hang of it it makes things much easier.
A lot of guy will just mark a line on the lathe bed with a Sharpie and use that as there indicator to disengage the half nut , I personally prefer the dial indicator.
Warner tools has some great HHS steel inserts if threading with a slower RPM is still desired.
threading is just one of those things that comes easier with practice , I'm not gonna admit to the amount scrap I've created in the last 23 years.
I've seen guys turn their cutter upside down and cut off the back side of the part in reverse because they were more comfortable than threading into a blind hole.
the biggest thing is find what works for you with the tools and machine you have and go with that.
the only advice I can give that I've never gotten any negative feedback from is invest in a good bench stone to finish off the edge of your tool , a few stokes with a 400 grit diamond laps will help a lot, after several cuts
Re: Single point threading titanium tube
Posted: Tue Apr 12, 2016 10:50 am
by Samson1044
T-Rex wrote:Damn Samson, you got some big nuts... errr Hands... errr nevermind

You know what they say about guys with big hands right!!!
Their gloves are tight.

Re: Single point threading titanium tube
Posted: Thu Apr 21, 2016 12:59 pm
by fishman
Not as good as samsons tube, but not bad for my first time machining titanium, or threading tube at all.
I took of .001" per pass and several cleanup passes at the end. 3 in 1 oil as lube. Roughly 150 rpm. Uncoated carbide.
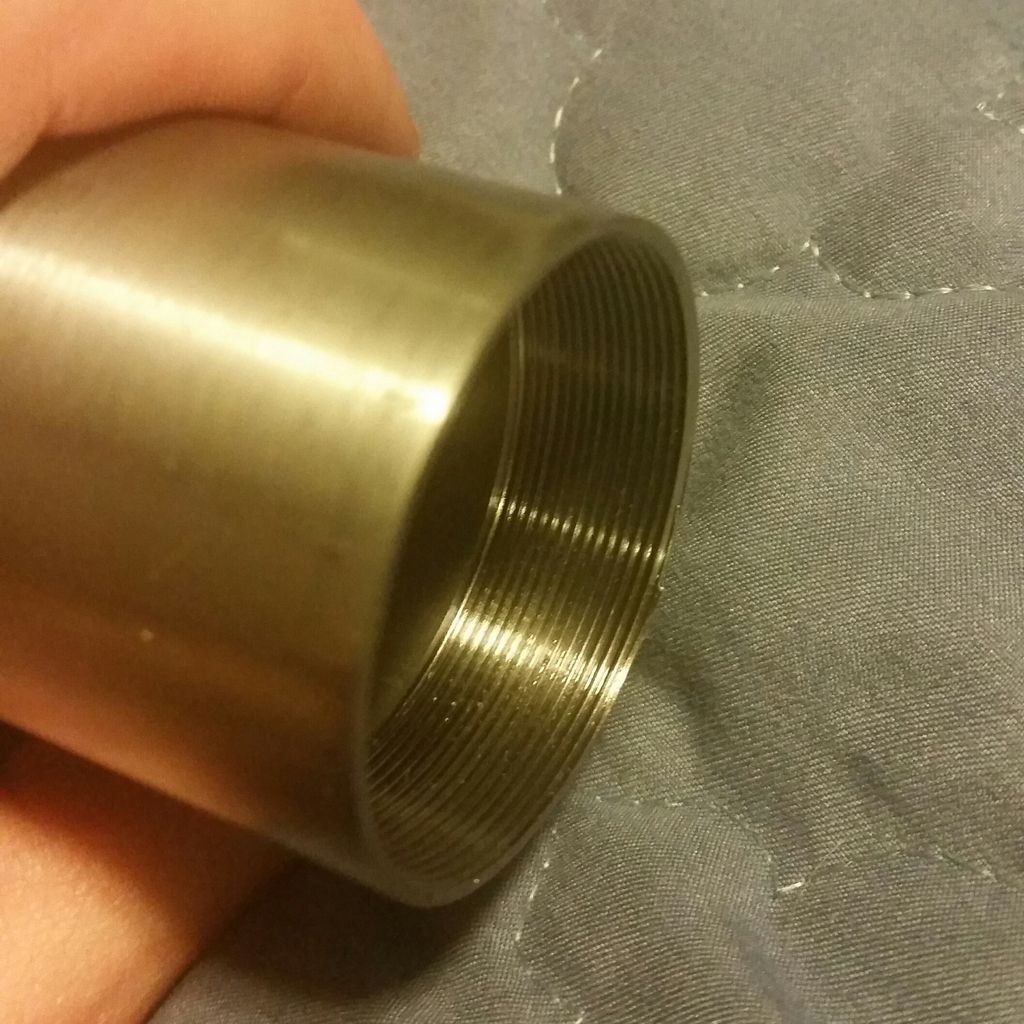
Re: Single point threading titanium tube
Posted: Thu Apr 21, 2016 1:17 pm
by propeine
fishman wrote:Not as good as samsons tube, but not bad for my first time machining titanium, or threading tube at all.
I took of .001" per pass and several cleanup passes at the end. 3 in 1 oil as lube. Roughly 150 rpm. Uncoated carbide.
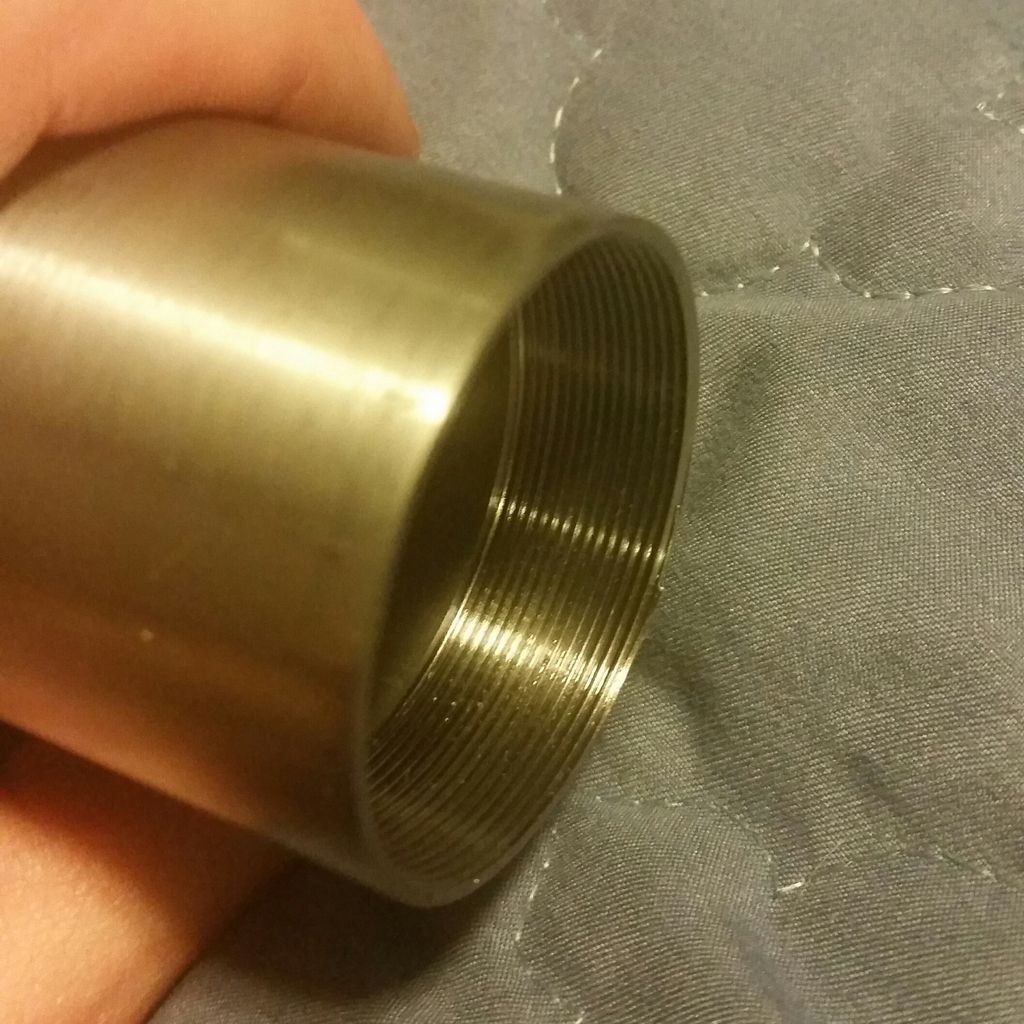
Threads look good! You may want to throw a small chamfer on there before you start next time so you don't have that first thread so thin it wants to tear out.
Re: Single point threading titanium tube
Posted: Thu Apr 21, 2016 1:23 pm
by fishman
propeine wrote:fishman wrote:Not as good as samsons tube, but not bad for my first time machining titanium, or threading tube at all.
I took of .001" per pass and several cleanup passes at the end. 3 in 1 oil as lube. Roughly 150 rpm. Uncoated carbide.
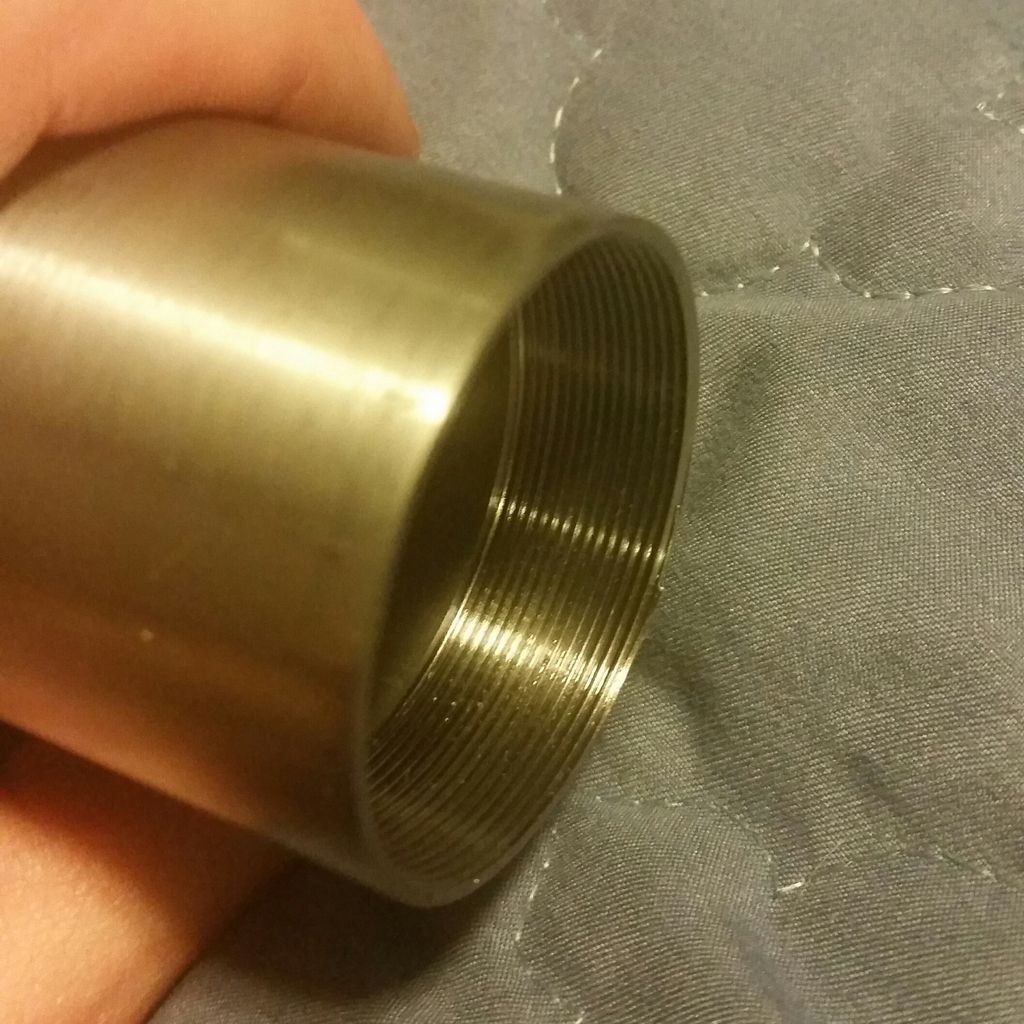
Threads look good! You may want to throw a small chamfer on there before you start next time so you don't have that first thread so thin it wants to tear out.
Thanks
Yeah, I forgot about doing that until after I started threading
Re: Single point threading titanium tube
Posted: Wed Apr 27, 2016 6:47 pm
by tommy69z
where are you guys getting your TI tube? I have some scrap SS .095 thick cut offs I had planned to use, but first threading attempt I discovered the thickness off a few thousands, planning now to try to cut end peices to try and thin/true up the tube...
Re: Single point threading titanium tube
Posted: Wed Apr 27, 2016 7:14 pm
by fishman
tommy69z wrote:where are you guys getting your TI tube? I have some scrap SS .095 thick cut offs I had planned to use, but first threading attempt I discovered the thickness off a few thousands, planning now to try to cut end peices to try and thin/true up the tube...
http://www.titaniumjoe.com/index.cfm/products/tubing/
Re: Single point threading titanium tube
Posted: Tue May 17, 2016 8:26 pm
by bstanga
I start threading at about the 6:00 mark. good luck
https://www.youtube.com/watch?v=j8KMdMKF0LQ
Re: Single point threading titanium tube
Posted: Wed May 18, 2016 6:57 am
by Historian
Modyfing Col. Kilgore* famous quotation:
"
... I love the smell of machine oil
cutting Titanium in the morning."
Brought back happy memories and smells for a freshman long
ago first day in the machine shop. And all those lathes, milling
machines, grinders, free metal. A guy's candy shop.
Nice tooling, nice work, Sir.
Thank you for invite.
* <<
https://www.youtube.com/watch?v=bPXVGQnJm0w >>